Instandhaltung 4.0: Die wichtigsten Trends
„Die Leistungen des Industrieservice tragen dazu bei, die Effizienz und Effektivität unserer Prozesse zu verbessern.“
Dieser Meinung sind 98 Prozent der Industrieunternehmen, die vom Wirtschaftsverband für Industrieservice (WVIS) in Deutschland für den Branchenmonitor 2017 befragt wurden. Fast ebenso viele geben an, dass Industrieservice einen hohen Wertbeitrag für die Industrie bringt. Dabei spielt die Instandhaltung eine wesentliche Rolle. So sagen 59 Prozent der für die Untersuchung befragten Dienstleister, dass Instandhaltungsleistungen der wichtigste und umsatzstärkste Teil in ihrem Portfolio sind. Zwar beleuchtet der Branchenmonitor nur die erbrachten Dienstleistungen – schliesst also die von Betreibern selbst durchgeführten Massnahmen gar nicht ein. Dennoch wird eines deutlich: Instandhaltung ist ein enorm wichtiges Feld.
Transformation zu Instandhaltung 4.0
Ein Feld, das sich durch Digitalisierung, Internet of Things und Industrie 4.0 erheblich wandelt. Ein Beispiel: Hersteller statten ihre Maschinen und Anlagen mit immer mehr Sensoren aus, die immer mehr Daten erfassen und diese via Internet weiterleiten. Damit muss sich zwangsläufig auch die Instandhaltung ändern – mit Blick auf die einzelnen Massnahmen, mit Blick auf die Qualifikationen der Menschen, die Instandhaltung erbringen, und mit Blick auf die Technologien, die für die Instandhaltung genutzt werden. Kurz: Parallel zur Industrie 4.0 muss sich eine Instandhaltung 4.0 entwickeln. Diese Dynamik in der Instandhaltung schlägt sich in vier Trends nieder:
Wertschöpfungsnetzwerk: Mit vereinten Kräften
Bei der Instandhaltung von Assets sind in der Regel drei Parteien beteiligt: Neben dem Betreiber sind das der Hersteller und der Instandhalter. Bei der Zusammenarbeit müssen sie zahlreiche Informationen untereinander austauschen. Und genau das war in der Vergangenheit ein Problem.
Ein Beispiel: Informationen zum Betrieb und zur Instandhaltung von Maschinen und Anlagen, Werkzeugen und Fahrzeugen stammen vom Hersteller. Bislang übermittelt der sämtliche technische Spezifikationen, Wartungshinweise und so weiter fast immer auf USB-Sticks, CDs oder sogar in Form von gedruckten Handbüchern an den Betreiber. Dieser legt die Informationen dann lokal im eigenen System ab. Problematisch ist das, weil die Hinweise damit isoliert bleiben. So können in manchen Fällen schon die eigenen Mitarbeiter nicht oder nur mühsam auf die Informationen zugreifen, die sie für den Betrieb benötigen. Für externe Instandhalter ist es so gut wie unmöglich, an die erforderlichen Hinweise zu kommen.
Auch an einer anderen Stelle hakt es: So sind mittlerweile fast alle Maschinen und Anlagen mit Sensoren ausgestattet, über die Daten erfasst werden, die auch etwas über den Zustand aussagen. Diese Daten stehen dem Betreiber zur Verfügung, der sie im besten Fall für die kontinuierliche Verbesserung der Prozesse nutzt. Hersteller und Instandhalter könnten die Maschinendaten zwar ebenfalls gut gebrauchen. Sie haben darauf aber nur in Ausnahmen Zugriff – zumindest ist das momentan so.
An den Schwierigkeiten beim Datenaustausch sollen künftig Wertschöpfungsnetzwerke etwas ändern. Die Kernidee: Betreiber, Hersteller und Instandhalter übermitteln ihre Daten – oder zumindest einen Teil davon – an cloudbasierte Systeme, auf die alle drei Parteien zugreifen können. Eine wesentliche Rolle spielt dabei der digitale Zwilling.
Digitaler Zwilling: Das virtuelle Spiegelbild
Der digitaler Zwilling – das ist das virtuelle Abbild eines realen Assets, dem sämtliche relevanten Informationen in digitaler Form zugeschrieben werden. Dazu gehören vor allem die Herstellerhinweise zu Betrieb und Instandhaltung, die Dokumentation zu allen Instandhaltungsmassnahmen während der gesamten Nutzungsdauer sowie die erfassten Maschinendaten. Dabei ist der digitale Zwilling deutlich mehr als eine Ansammlung von Informationen. Das jeweilige Asset wird auch abgebildet – beispielsweise mit Fotos und 3D-Modellen.
Damit ist der digitale Zwilling in einem Wertschöpfungsnetzwerk quasi das verbindende Element zwischen Betreiber, Hersteller und Instandhalter. Das virtuelle Abbild leistet aber noch mehr: Weil die Maschinendaten in Echtzeit erfasst werden, können die laufenden Prozesse eins zu eins abgebildet und sogar visualisiert werden. Für das Condition Monitoring – das von einigen, aber noch längst nicht allen Unternehmen eingesetzt wird – ergeben sich daraus neue Chancen. Ausserdem lassen sich mithilfe des digitalen Zwillings Abweichungen vom Normalbetrieb, die möglicherweise zu Störungen führen, simulieren. Betreiber können dann frühzeitig Präventionsmassnahmen ergreifen. Und schliesslich ist der digitale Zwilling Ausgangspunkt für neue Services und Geschäftsmodelle – wie beispielsweise Predictive Maintenance. Voraussetzung dafür ist, dass die Daten systematisch und gezielt ausgewertet werden.
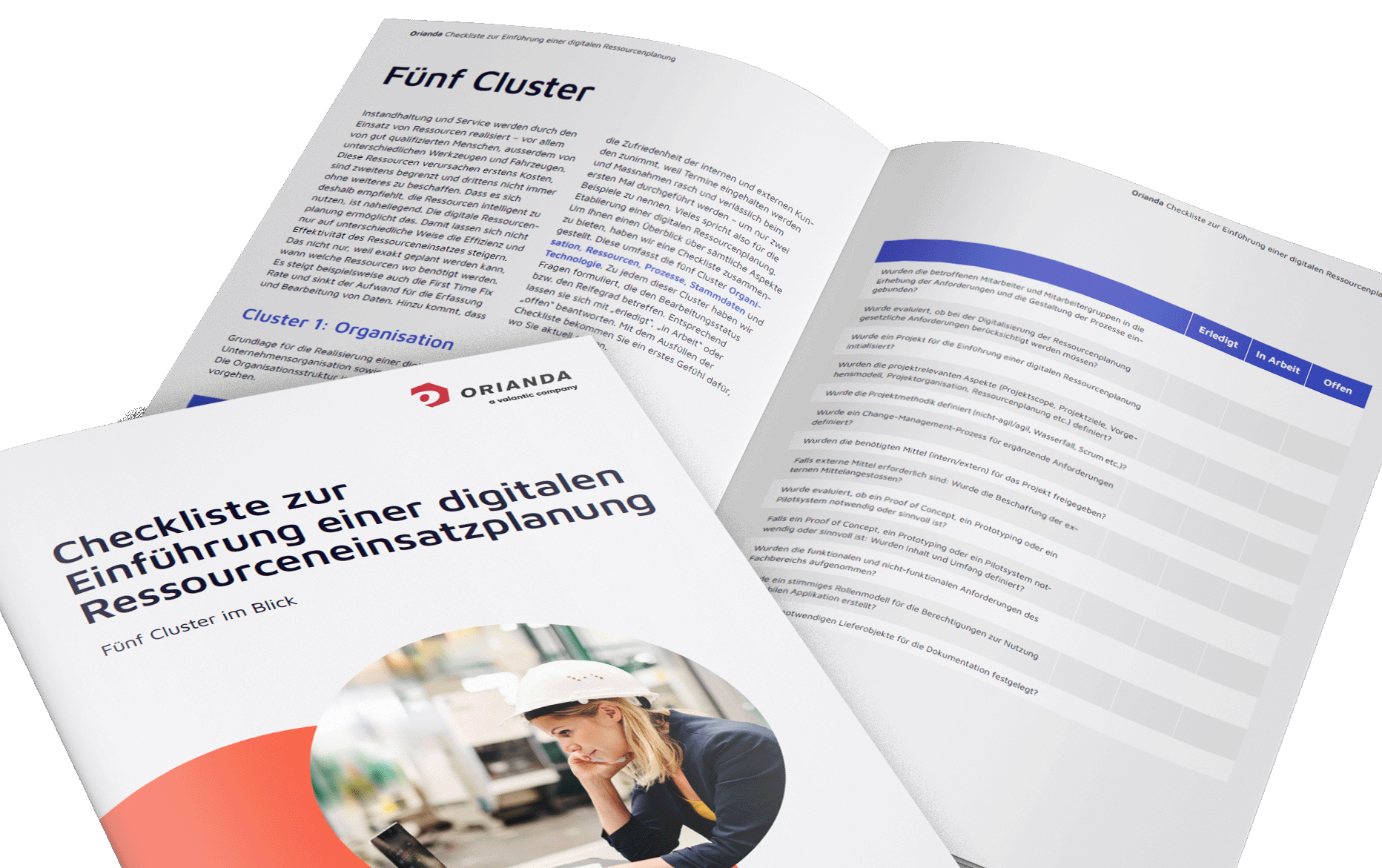
Checkliste: Einführung digitale Ressourcenplanung
Wenn Unternehmen mithilfe innovativer Technologien ihre Ressourcenplanung digitalisieren, realisieren sie damit einen erheblichen Mehrwert. Worauf Sie achten sollten, haben wir in unserer Checkliste zur Einführung von digitaler Ressourcenplanung zusammengestellt.
Data Science: Die Wissenschaft der Datenauswertung
Mit Sensoren ausgestattete Assets generieren riesige Datenmengen, die ihren digitalen Zwillingen zugewiesen werden. Das allein ist schon ein echter Fortschritt. Damit aus den Daten aber noch mehr nützliches Wissen wird, sind leistungsstarke Analyseverfahren erforderlich. Vor diesem Hintergrund wird Data Science immer wichtiger. Data Scientists beschäftigt sich unter anderem mit Data Mining, Machine Learning, Operations Research und Statistik. Diese quantitativen Methoden nutzen sie zum Beispiel, um in zunächst chaotisch erscheinenden strukturierten und unstrukturierten Daten der Vergangenheit Muster zu erkennen. Auf Basis dieser Muster und mithilfe von Algorithmen, die aktuelle Daten in Echtzeit mit multivarianten Analysen auswerten, lassen sich dann etwa Prognosen erstellen. Ein konkretes Einsatzszenario dieser performanten Datenauswertung ist Predictive Maintenance.
Predictive Maintenance: Der Störung einen Schritt voraus
Predictive Maintenance ist ein Schlüsselthema für die Industrie. Denn durch die Analyse von gesammelten Maschinendaten lässt sich die voraussichtliche Entwicklung des Zustandes eines Assets errechnen und können mögliche Störungen frühzeitig prognostiziert werden. Auf diese Weise lassen sich ungeplante Ausfälle vermeiden und erforderliche Instandhaltungsmassnahmen optimal planen. Für die Betreiber ist damit eine erhebliche Verringerung der Kosten verbunden – ebenso eine Steigerung des Outputs. Für Hersteller und Instandhalter kann Predictive Maintenance eine Möglichkeit sein, das Leistungsportfolio um neue Services zu erweitern.